使用实时分析杜绝生产浪费
低产量、品种多样而独立的制造商要在数小时,甚至数分钟内完成装配线改造,以迎合不同的生产要求。这些装配线要连接运行数天或数个班次,期间哪怕发生最不起眼的故障,都会对产量和盈利造成重创。
除此以外,还会产生大量的废料和浪费,推高制造商的经营成本。那么,提高生产效率到底有多重要?数百万美元的成本节省,其意义不言自明。
在接受麦肯锡全球调查的高管中,68 % 的受访者认为 “数字化制造” 是他们组织的首要任务。因此,制造商纷纷投资新技术,从工厂车间到数据分析等等,以提高工厂效率和改善修复流程。
例如,使用实时分析,一家工厂优化了金属喷涂工艺,减少了缺陷和返工率——将首次合格率从 35% 提高到 96%,每年为企业节省 50 万美元。
另一家工厂优化了隔膜制造工艺——废料减少 40%,产量提高 47%。通过在传统工厂中部署实时分析,该公司成功将运营开支控制在 90 万美元,同时显著提高产能。
AI 推动制造业迈向工业 4.0
为了实现这些运营改善,制造商需要掌握在工厂车间产生的所有数据,从传统机器到先进设备,对整体情况了如指掌。考虑到大多数工业设备在设计上没有数字共享功能,这给实时查看和决策制定设置了障碍。
霍尼韦尔 Tridium 的全球市场开发副总裁 Mike Luscombe 说道:“他们需要通过某种方式来收集和标准化各种不同机器生成的所有数据,从而实时、准确地了解各种工艺和运营的现状。”
专业开发人员运用工业流程、AI、数据系统和时间敏感网络 (TSN) 方面的知识来创建精密的解决方案,将不同的制造数据转换为一种常见且可衡量的数据。
为此,霍尼韦尔 Tridium 公司的与戴尔和英特尔® 携手开发了 Niagara4 i4.0 工厂优化解决方案。该系统包括一个完整的硬件和软件堆栈,能够承受工业环境中的恶劣条件。该解决方案结合了 Niagara Framework——在可靠的 Dell Edge 网关上运行的开放技术平台,如图 1 所示。
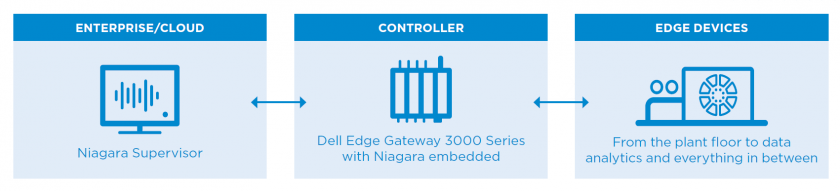
“该系统通过各种传统机器上的传感器收集边缘数据。然后,软件将数据标准化,再将相关信息上传到云,” Luscombe 说道,“这让制造商站在一个以前无法企及的高度来审视运营情况。”
此外,该软件还可以自动修复,迅速纠正问题。例如,在工厂车间中,机器操作员可以在仪表板上查看实时数据,并立即判断设置是否正确校准,公差是否符合规范。经理还可以查看总体生产数据,以了解生产是提前还是落后于计划,并根据需要采取行动来确保各项工作有序进行。
使用分析功能提高产量
Luscombe 举了一个例子来说明:一家航空航天产品制造商如何在使用高压釜生产飞机刹车部件的碳纤维制造工艺中提高产量。“在使用 Niagara 解决方案后,该公司很快发现,当地公用事业公司的天然气源的成分不一致。这使得制造商几乎不可能在高压釜中保持适当的条件。这样造成了极低的产量。”
得知天然气成份不一致这一简单事实后,管理层恍然大悟,开始自动调整制造工艺和配方,以适应燃料质量的任何变化。这一发现的结果带来了 89% 的增产,以及 250 万美元的运营成本节约和 200 多万美元的资本支出成本规避。
专注边缘设备,走在技术前沿
Luscombe 说:“我们在全世界部署了将近 80 万个 Niagara。早在边缘数据处理普及之前,我们一直在为边缘应用程序开发软件。随着 IIoT 技术的发展和处理速度的加快,我们致力运用专业知识和见解在数据与新行业之间建立联系,创造有实际意义的成果。”
Niagara 解决方案为制造商提供了跟踪和显示 KPI 的功能,如总体设备效率 (OEE)、轧制产量 (RTY) 和低质量成本 (COPQ)。此外,该解决方案还可以通过可视化工具和智能数字化表单帮助制造商优化工作流。公司还可以使用该解决方案处理实时和历史趋势数据,从而准确地执行各种任务,包括检测缺陷、跟踪部件和管理配方。
数据收集是 Niagara 的重要组成部分,该解决方案不依赖于云,遵循行业最佳网络安全实践。包括支持强散列密码、用于安全通信的 TLS v1.2 和用于身份验证的证书管理工具等功能。
Niagara 还将开放的边缘到云连接用于多种用途,包括传感器、可编程逻辑控制器、机器和 ERP 系统。它还提供嵌入式边缘分析功能和开放式应用程序环境,为机器操作员和工厂经理提高可行的见解,帮助他们提高工作效率。
使用实时分析取得 4.0 硕果
对于低产量、品种多样而独立的制造业而言,速度和短生产周期是常见挑战,如果不能迅速纠正故障,情况将日益恶化。通过收集各种设备和机器生成的数据并将其标准化,制造商最终能够实时了解工厂车间的工艺和操作,并迅速采取修复措施。
Luscombe 说:“通过在传统设备上运行边缘分析,制造商可以利用新的机会提高效率,降低制造成本,从而获得巨大的运营收益。”